Intervista a Michele Pedroni, co-fondatore con Stefano Giussani di Pedroni Race, che segna il ritorno in grande stile di una storica realtà della mountain bike gravity
Il primo modello a essere introdotto a un anno dalla rinascita è Mate, una affascinate e performante enduro con telaio in carbonio e in alluminio, interamente realizzata in casa, dalla progettazione al costruzione.
Pedroni Mate, che presto troverete in prova su 4Bicycle, sfrutta il retaggio ventennale di Michele Pedroni nel movimento downhill ed enduro.
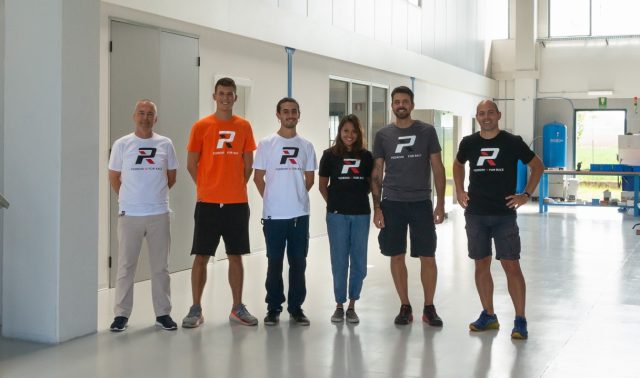
Pedroni Race: la storia
Tutto nasce a fine anni novanta, per la precisione tra il 1998 e il 1999, quando Michele Pedroni – allora 18enne – inizia a costruire, insieme al fratello Marcello e al padre Ernesto, le prime bici Pedroni Cube e crea il Racing Team Pedroni Kjub, correndo con i propri prodotti.
Facciamo un deciso passo in avanti nel tempo, arrivando al 2013, con la nascita di Movetech Srl e il marchio Pedroni Cycles. La gamma si è già differenziata e ampliata, passando dal downhill delle origini al più attuale enduro. In questo periodo Michele inizia ad acquisire una forte competenza sui telai e in particolare sulla lavorazione del carbonio. Sono gli anni della Lupo Carbon Gara, provata nel 2016.
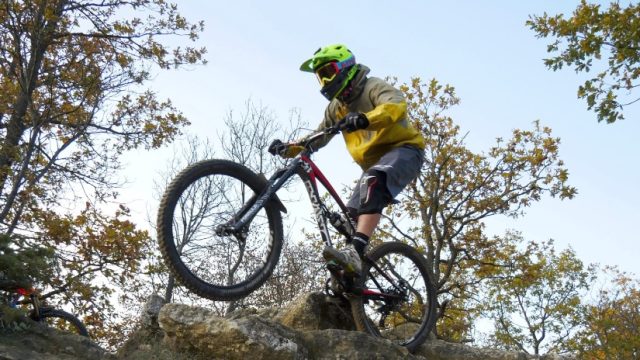
I risultati non mancano, finendo più volte a podio e vincendo titoli nazionali e internazionali: Michele è campione italiano DH Master nel 2010, vincendo il Gold Prix l’anno successivo; il padre Ernesto conquista la maglia iridata Master nel 2016; nel frattempo vince la classifica assoluta del trofeo Gravitalia nel 2014, mentre l’anno successivo è Tommaso Francardo a conquistare la vetta tra gli Under 23 in quella che per anni è stata la principale serie nazionale dedicata al downhill.
Cinque anni dopo, nel 2018, arrivano le prime eMTB, un progetto che matura con quella E-Pard motorizzata Polini – introdotta nel 2020 – che tanto ci era piaciuta quando l’avevamo provata (qui il nostro test).
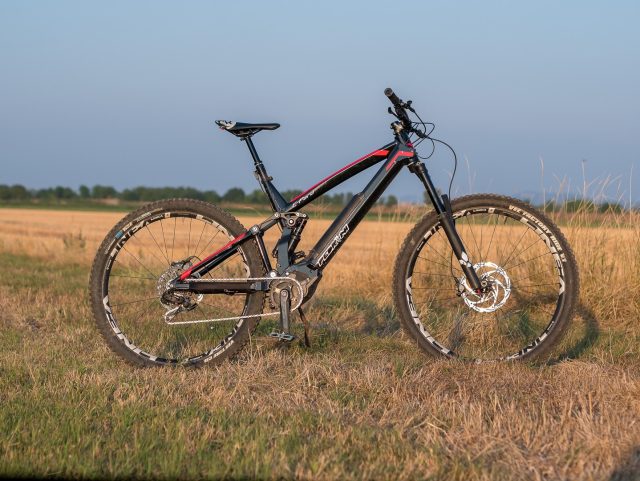
La vita è fatta di alti e bassi, Movetech chiude ma i fan non disperano… infatti, nel 2021 Michele e Stefano Giussani fondano Pedroni Race, ricoprendo i rispettivi ruoli di direttore tecnico/operativo e amministratore delegato.
Si passa da una realtà artigianale a una più strutturata, ma sempre con la chiara impronta delle origini: bici pensate da appassionati e dedicate agli appassionati che vogliono competere nei campi gara enduro e DH. Ma non solo, la volontà è di estendere il bacino d’utenza anche al di fuori dei nostri confini, con un piano di crescita ed espansione pluriennale.
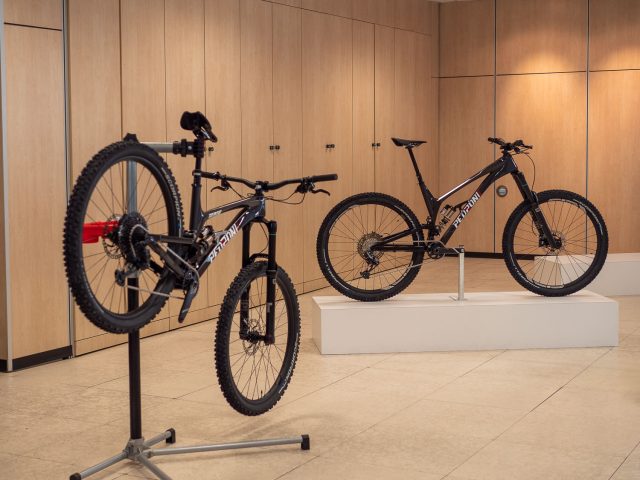
Pedroni Race: il presente
Il focus di Pedroni Race sta nel mix tra esperienza pregressa nella progettazione e costruzione di telai, oltre a quella maturata nei campi gara, e nell’innovazione applicata ai materiali compositi. Trait d’union è il controllo qualità totale, essendo il tutto pensato, progettato, realizzato e provato in casa, così da garantire un prodotto non solo efficiente ma anche resistente in condizioni di utilizzo estreme.
Da questo punto di vista, ma anche da quello di gestione dell’attività, il contributo dell’amministratore delegato e co-fondatore Stefano Giussani è fondamentale: vanta 17 d’anni d’esperienza nel settore aerospaziale, con competenze manageriali a 360° focalizzate su innovazione e digitalizzazione.
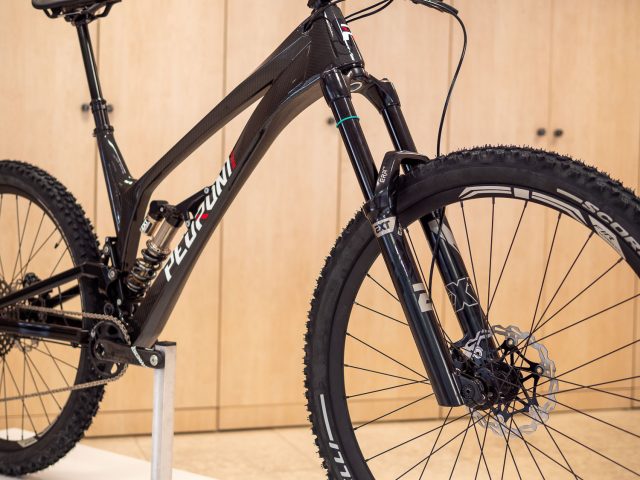
La collocazione sul mercato è nella fascia alta, con componenti e tecnologie innovative, puntando anche nell’allestimento al Made in Italy. I segmenti di destinazione sono ovviamente downhill, enduro ed e-enduro. Il primo progetto ad arrivare sul mercato è quello identificato inizialmente con la sigla M8, e che ha preso il nome di Mate, una moderna mountain bike enduro. Seguiranno il progetto “Fusiosa Legacy” da DH (di cui è stato depositato il brevetto), e la e-Enduro “Charger”.
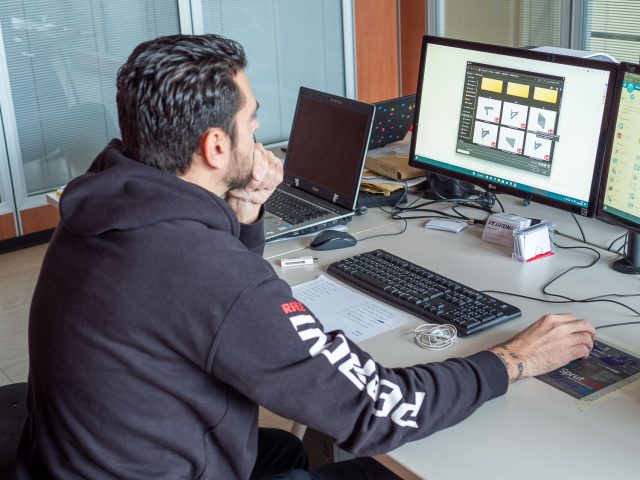
Dalla mente ai sentieri: come nasce Pedroni Mate
Abbiamo raggiunto Michele e Stefano nella sede operativa di Reggio Emilia, per una lunga, ampia e struttura intervista su cosa caratterizza Pedroni Race e come è nata Mate, dalle prime immagini visualizzate nella mente al prodotto fatto e finito, pronto per essere messo alla prova sui sentieri enduro più sfidanti.
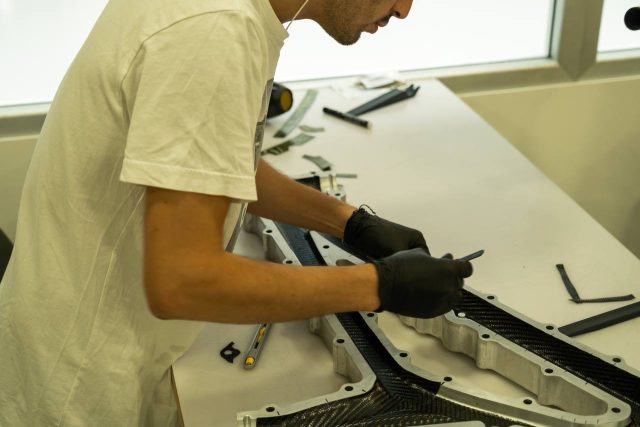
“Rispetto al passato sicuramente c’è una grossa differenza a livello di capacità organizzativa e soprattutto di struttura. Abbiamo internalizzato completamente la produzione, quindi dal reparto saldatura a tutti i particolari in CNC e anche la produzione interna di stampi sempre con col centro di lavoro, e ci siamo anche resi indipendenti con tutto il discorso della laminazione del carbonio.”
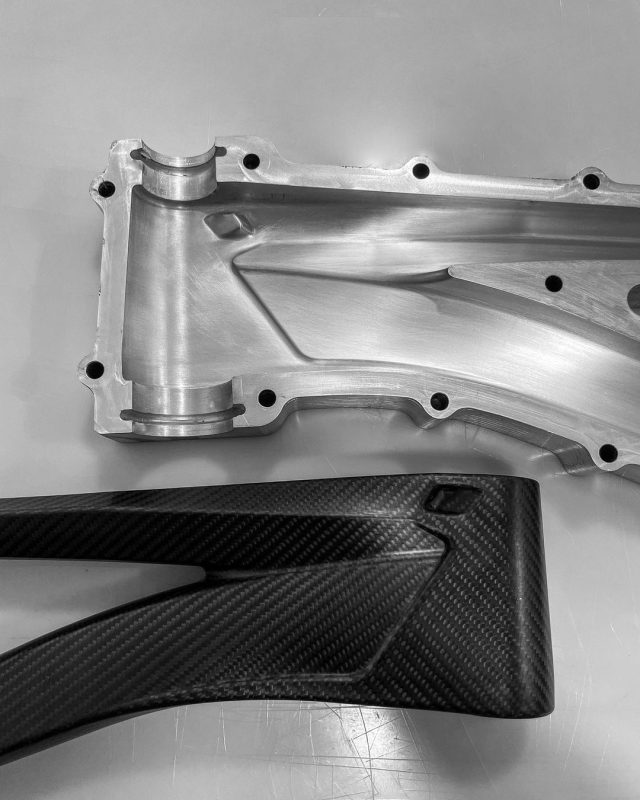
“È un reparto molto impegnativo perché comunque comprende varie differenti attività e diversi macchinari: si passa dal taglio pelli con un plotter automatizzato all’autoclave, quindi aspetti piuttosto differenti rispetto a quelli che storicamente avevamo affrontato finora.”
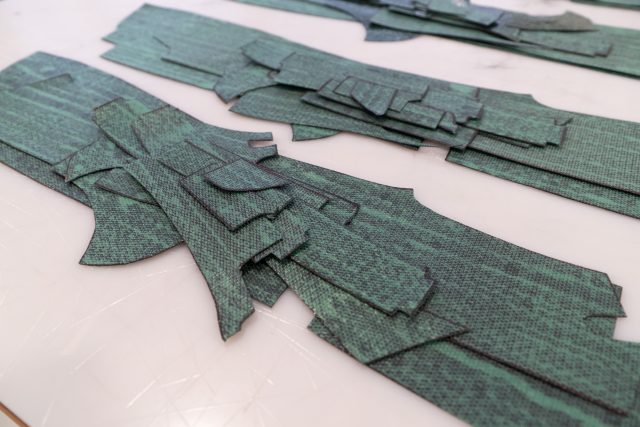
“Il background non ci manca, semplicemente prima non riuscivamo a gestire internamente la progettazione e anche la produzione del carbonio. Adesso le possibilità sono completamente diverse, è una struttura piccola ma estremamente preparata.
Rispetto alla concorrenza abbiamo una struttura più snella, ma proprio perché più snella riusciamo anche avere tempi i tempi di reazione e produzione differenti, aiutati sicuramente anche dal fatto che la produzione appunto è completamente interna.”
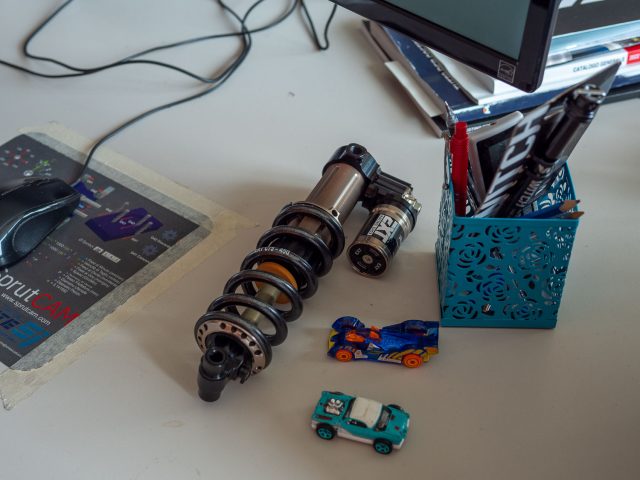
Il progetto del telaio
“Innanzitutto il progetto parte dal comportamento che si vuole poi ottenere sui sentieri, quindi c’è un lungo studio della cinematica della sospensione posteriore. Fatto questo, si cerca di integrarlo e ottimizzarlo a livello di design.”
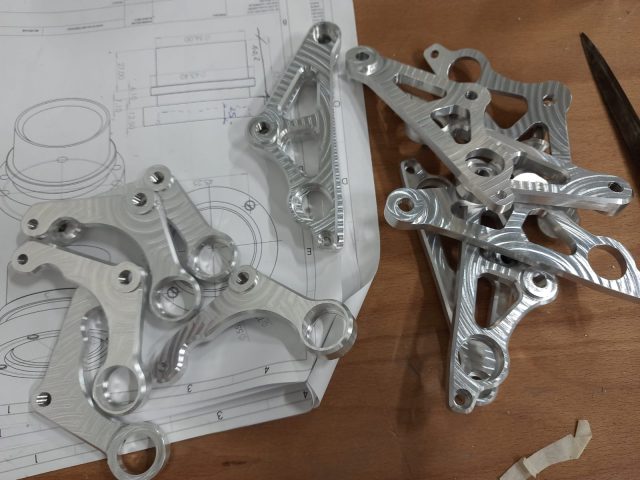
“È un po’ come il discorso di una scultura, tanti piccoli pezzi vengono portati avanti tutti insieme fino a creare quello che poi diventa il risultato finale. Quindi si inizia con il discorso progettazione, che già si divide in due parti: abbiamo il triangolo anteriore in carbonio e il carro posteriore in alluminio. Sono due tipi di progettazione differenti da portare avanti in parallelo.”
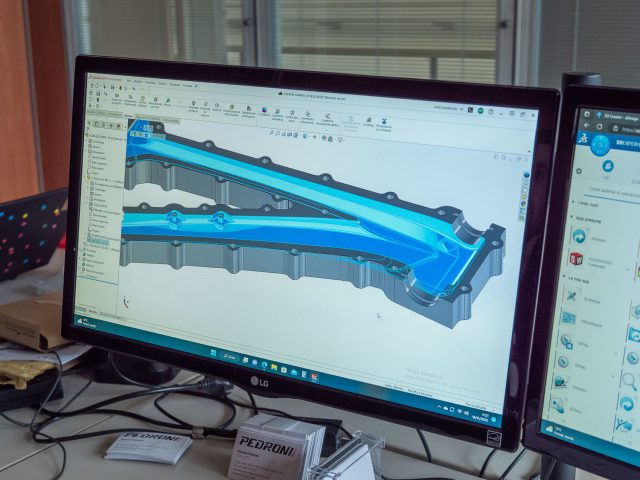
“Chiaramente la progettazione del carbonio riguarda molto il design, unito alla funzionalità, a cui dopo si deve applicare comunque il piano di laminazione: quante pelli, che tipo di grammatura, e con quali intrecci. Vanno a comporre il cocktail delle pelli di carbonio, mentre sull’alluminio abbiamo un po’ meno libertà di design, però cerchiamo sempre di usare i migliori materiali a disposizione.”
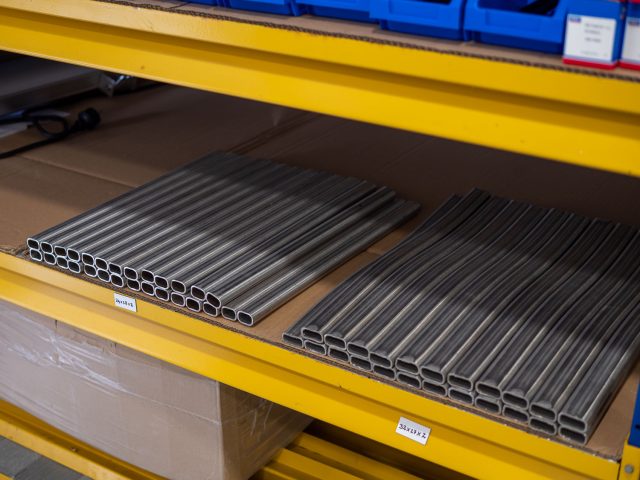
“Il carro posteriore è tutto realizzato in alluminio 7020, che a livello meccanico è la miglior lega saldabile a disposizione. Tutti i leveraggi sono un’altra parte da affrontare a livello progettuale, insieme al boccolame viene tutto realizzato in Ergal, la lega con le capacità meccaniche sicuramente più elevate. Tutti questi aspetti vengono portati avanti insieme, anche ovviamente alla progettazione delle dime per la saldatura così da ottimizzare tutto il processo.”
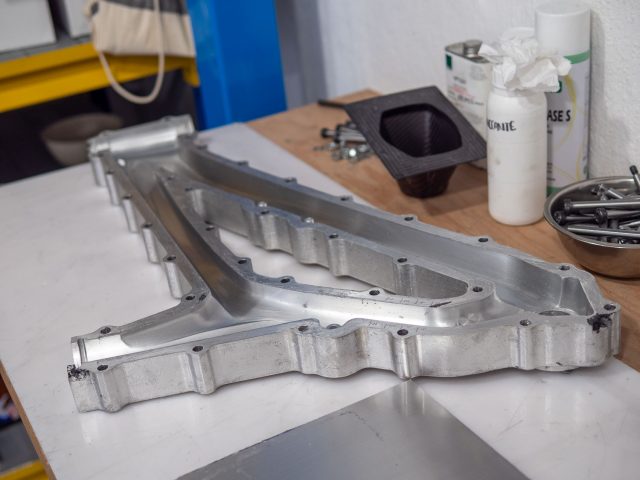
“Terminato il processo di progettazione, si passa a quella dello stampo per la produzione del carbonio. Ultimati i disegni, si procede con i programmi CAM, che vengono portati in macchina, dove viene realizzato lo stampo diviso in due semigusci. Dopodiché si passa alla preparazione dello stampo con i relativi prodotti, quindi distaccanti eccetera, da qui si passa alla laminazione, dopo aver affrontato tutto il discorso delle dime, quindi le forme che queste pelli devono avere per adagiarsi perfettamente nello stampo.”
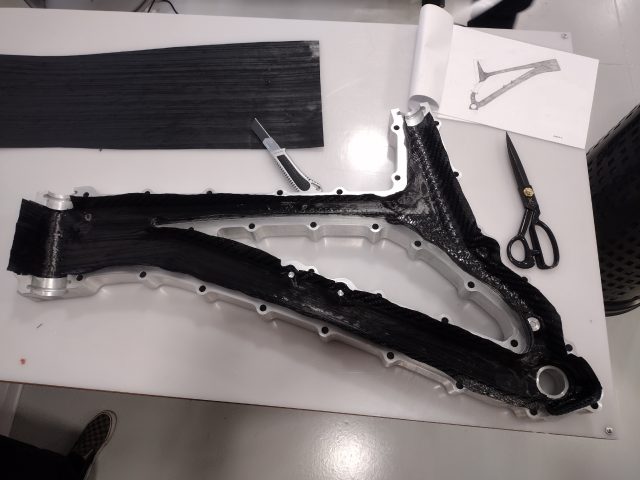
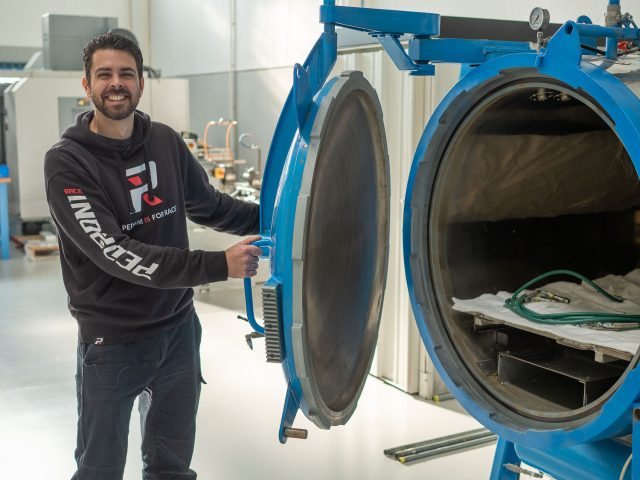
“Finita la fase di laminazione, con un sistema di sacchi interni più un sacco esterno, si isola lo stampo che poi viene portato in autoclave. Questo ha un “ciclo di cura” ben preciso, che viene comunque indicato dai fornitori di carbonio. Finita la cotta in autoclave, il triangolo anteriore viene prima estratto e poi rifilato.”
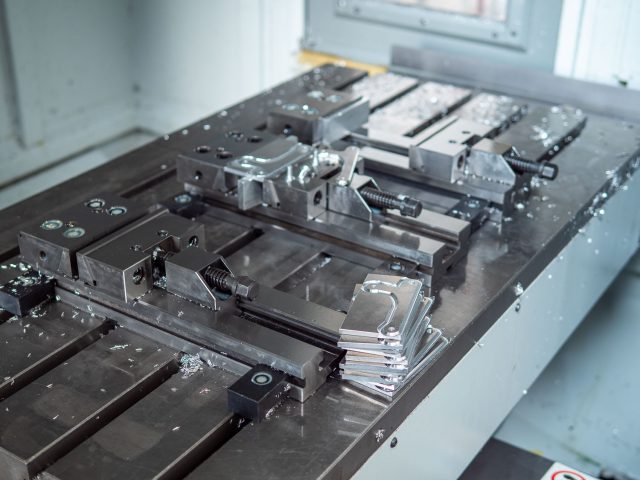
“Per quanto riguarda invece caro posteriore, vengono acquistati dei tubi Dedacciai, quindi di produzione italiana, in 7020, che vengono saldati nelle dime di nostra realizzazione con particolari lavorati con le nostre macchine, sempre in 7020. Successivamente il carro posteriore viene sottoposto a un ciclo termico nel forno, dopo è pronto per essere spedito in verniciatura, l’unica operazione che è fatta esternamente. Tutto il gruppo leveraggi viene prodotto sempre internamente e poi viene mandato in anodizzazione, un altro trattamento esterno.”
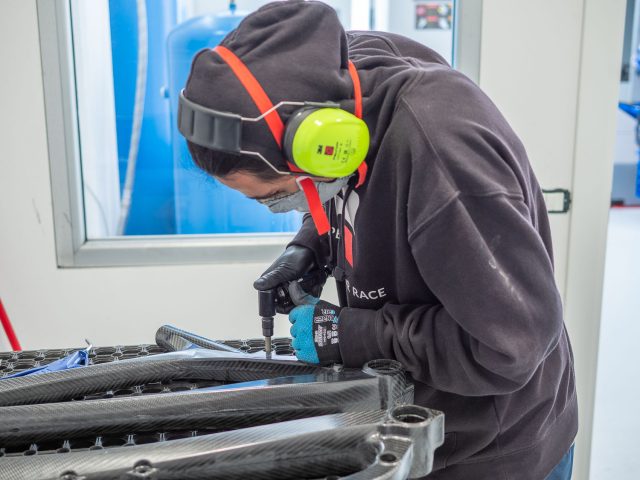
“Alla fine il telaio è pronto per essere assemblato prima e per montare la bici poi, che infine viene consegnata o al cliente direttamente, che può sia ordinarla online sia qui in azienda, oppure attraverso uno dei nostri punti vendita selezionati, che curano in modo particolare il cliente.”
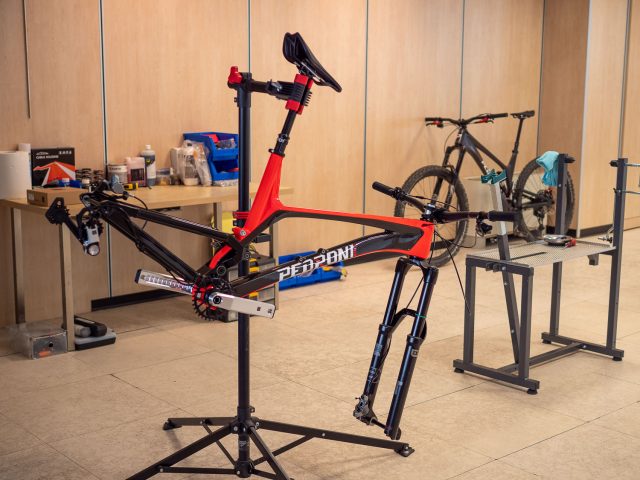
“Questa è la nostra filosofia, quella di lavorare con persone che riescano a essere all’altezza dello studio che c’è dietro a un prodotto di questo livello e utilizzo.”
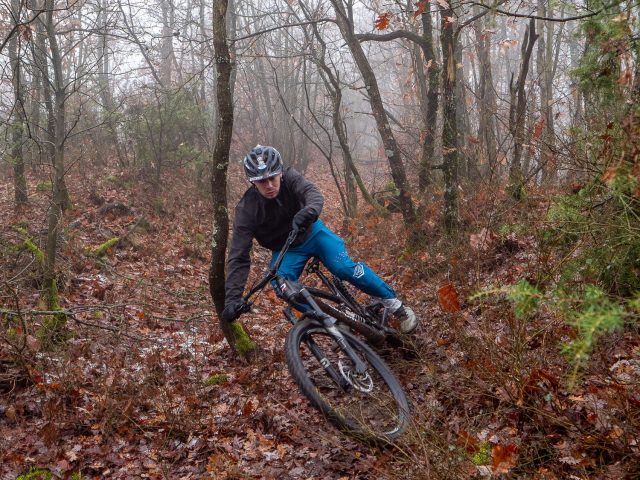
Pedroni Mate: il test
Abbiamo ricevuto una bici Pedroni Mate in test, che si presenta da subito come una modernissima enduro, tranquillamente in grado di strizzare l’occhio a un uso in bike park o comunque un utilizzo discesistico intensivo.
170 mm è il travel della sospensione posteriore MateXP pareggiati all’anteriore, queste le principali quote geometriche: angolo sterzo di 64,5°, angolo sella di 76°, carro lungo 439 mm, movimento centrale alto 345 mm con drop di 25 mm, reach da 430 a 505 mm e stack da 617 a 641 mm sulle quatto taglie (da S a XL, altezze consigliate da 158 a 195 mm).
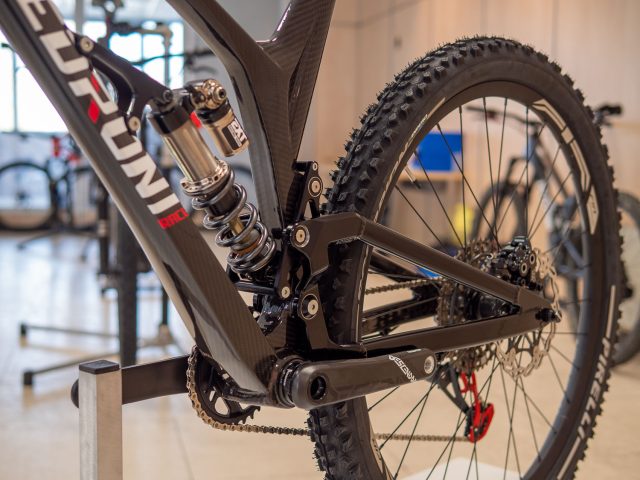
La piattaforma posteriore ha un’ottima resa in pedalata, in salita la sospensione si stabilizza, offrendo un supporto adeguato per risparmiare energie lungo i trasferimenti delle gare enduro.
La guida di questa bici risulta semplice dal primo utilizzo. Una volta messi a punto appoggi e sospensioni, viene tutto molto naturale. È intuitivo scegliere qualsiasi linea, anche nelle pietraie più impegnative si possono fare continui cambi e correzioni con un grande facilità.
Il retrotreno rimane inoltre stabilissimo quando viene estremamente sollecitato, quindi anche da qui la facilità che si ripercuote sulla guida. È un telaio che appare molto sincero e “comunicativo”, sia in ingresso sia in tutta la percorrenza e in uscita di curva. Il carro posteriore sembra inoltre rigido, ma senza eccedere, riuscendo a offrire in ogni caso un buon comfort nella lettura delle asperità del terreno.
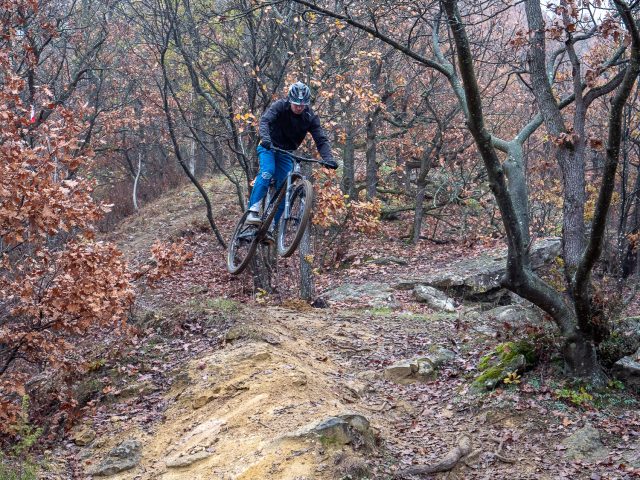
Il frameset è abbinato a sospensioni Extreme Shox – forcella Era V2 ad aria e ammo Storia Lok V3 a molla – un’azienda che da sempre fa del Made in Italy il suo fiore all’occhiello. Il comportamento con questo ammortizzatore è molto bilanciato, grazie anche all’idraulica messa a punto appositamente per la Mate. Questo è un altro grosso vantaggio di poter lavorare con un’eccellenza del genere.
La bici si divora le grandi asperità e al tempo stesso risulta molto reattiva nel momento in cui ci si va appoggiare in sponda o quando si deve pompare per saltare.
Il test è appena iniziato, per ora siamo molto soddisfatti, perché stiamo trovando quello che per noi è il bilanciamento ottimale nella guida, nella risposta delle sospensioni, e nella solidità del telaio, per un reale utilizzo enduro senza compromessi.
Info: pedronirace.com
[foto: Cristiano Guarco | rider: Francesco Marchese | spot foto action: Monte San Vito Trail Area]