Foto: Martina Folco Zambelli/HLMPHOTO
Per tornare a produrre telai in Italia, senza perdere in competitività nei confronti dell’Asia, bisogna rivoluzionare il ciclo produttivo. Non c’è alternativa… È quello che ha fatto 3T e, in che modo, siamo andati a scoprirlo.
In questo viaggio, il nostro Virgilio – anche sa sarebbe meglio dire Beatrice, dato che ci siamo addentrati in una specie di Paradiso – è stato Enrique Romero Pineda, responsabile di produzione di 3T. Ingegnere aerospaziale con un bagaglio di esperienza nella lavorazione della fibra di carbonio, è colui che ha organizzato la nuova factory di Presezzo (BG), nella quale sono realizzati i modelli top di gamma, con l’obiettivo di riportare in Italia l’intera produzione, ora delocalizzata in oriente, entro un paio di anni.
Perché avete deciso di tornare a produrre in Italia?
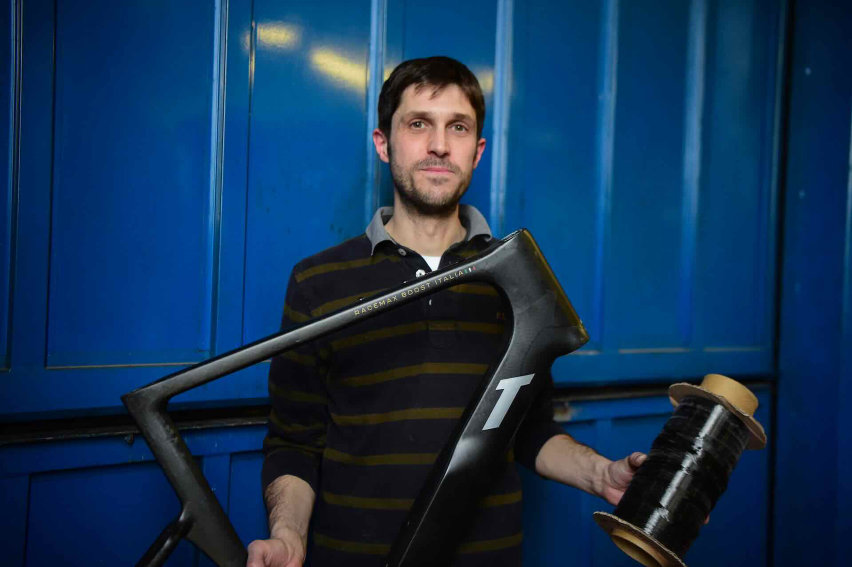
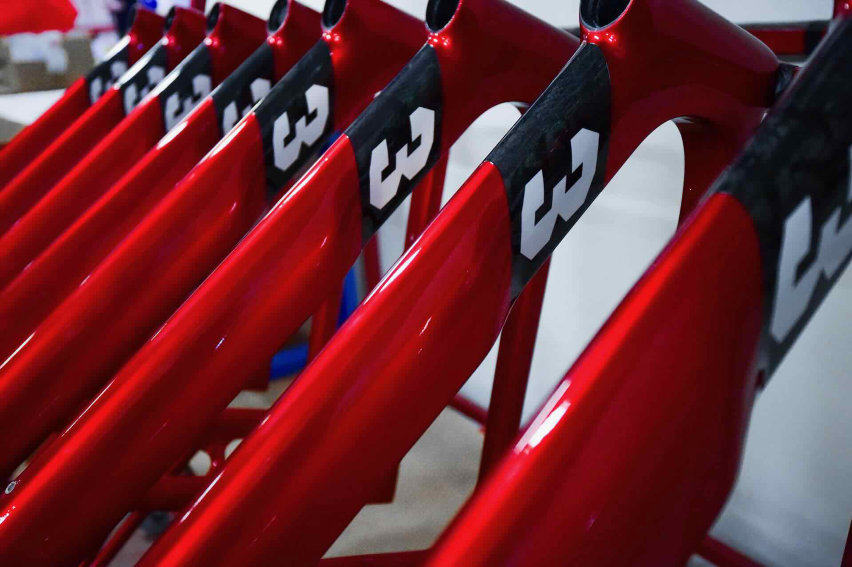

“I motivi sono vari e vanno oltre l’orgoglio del Made in Italy. Ci sonno anche la volontà di essere più competitivi e di avere maggior controllo sulla qualità del prodotto. Ogni telaio è infatti tracciabile in tutte le fasi di produzione e questo ci permette di raccogliere dati che ci aiutano a capire e a migliorare il processo stesso e a intervenire anche nel controllo di qualità, il tutto con tempi di reazione praticamente azzerati.“
Come è avvenuta la riorganizzazione del lavoro?
“Il primo passo è stato analizzare ogni fase della lavorazione dei telai, per capire se e come potesse essere ripensata in ottica italiana, per adattarla ai nostri obiettivi e alle dimensioni di una piccola realtà come 3T.
Successivamente, una volta capito come procedere, abbiamo dovuto modificare o costruire ex-novo alcuni macchinari indispensabili per il nuovo metodo di produzione.
Abbiamo cominciato a internalizzare i modelli di fascia alta e contiamo, entro breve, di portare in casa tutta la produzione.“
In cosa differiscono i due processi di lavorazione?
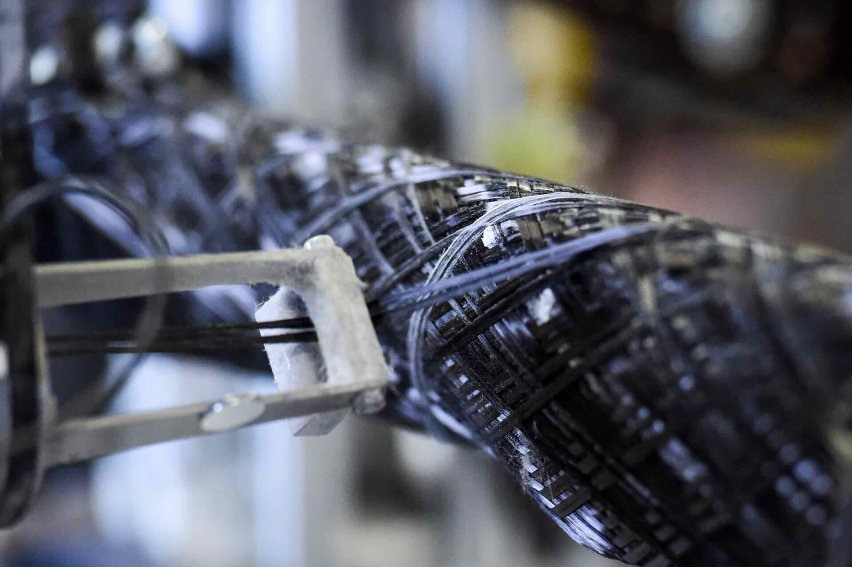
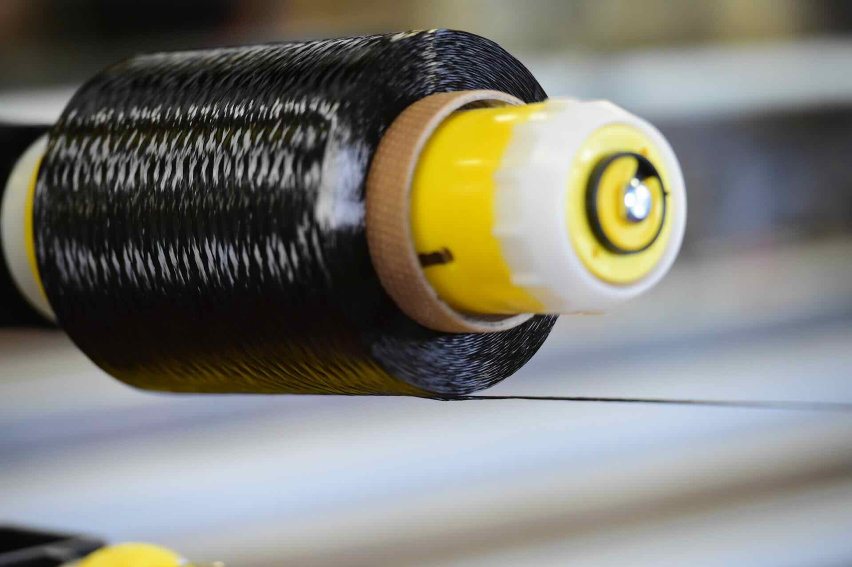
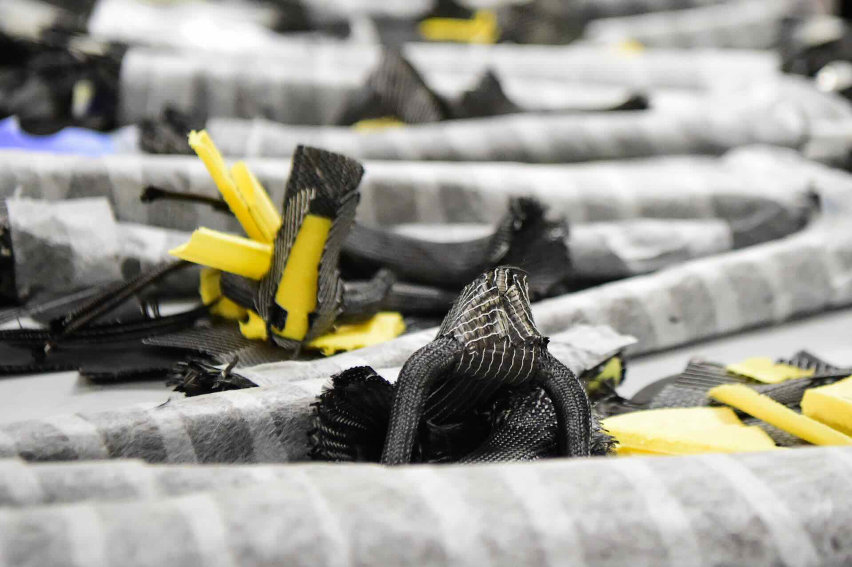
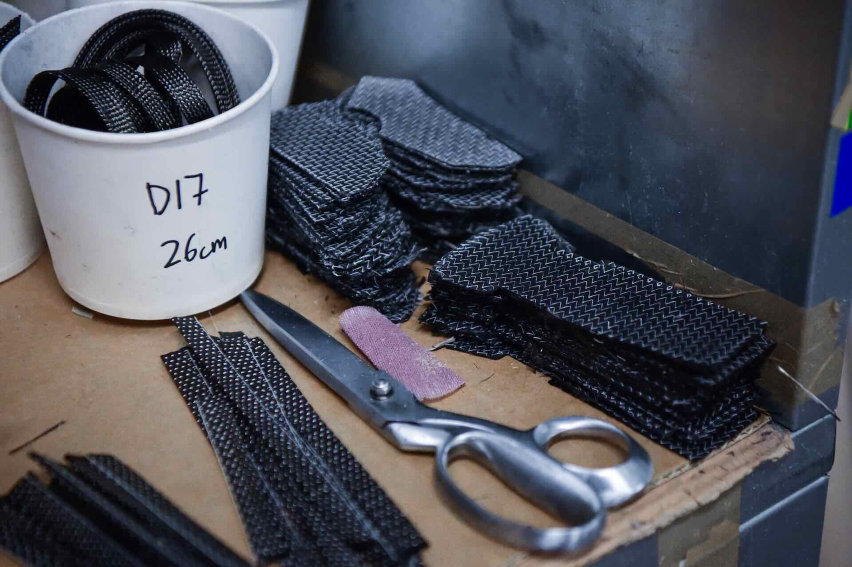
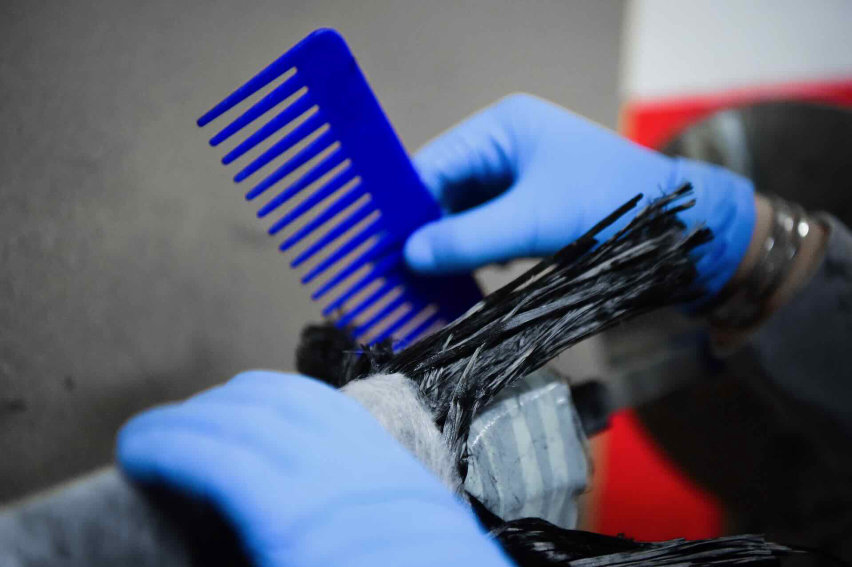
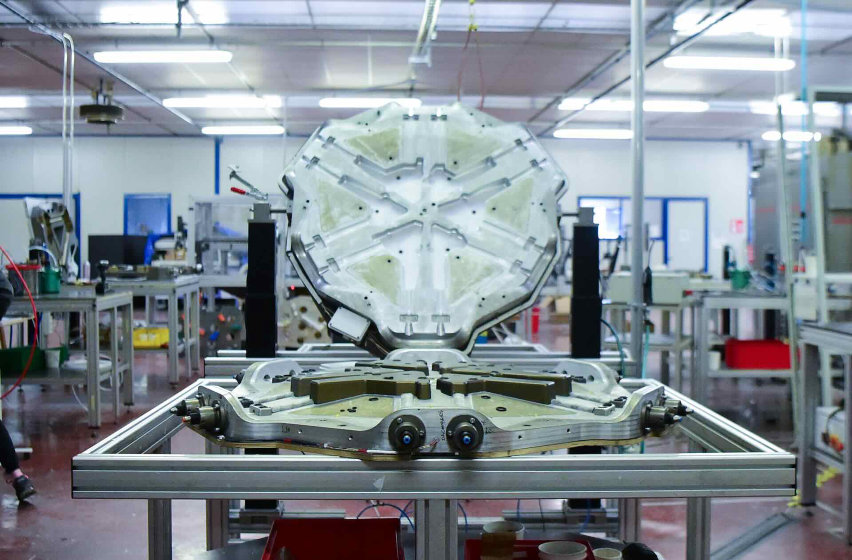
“La più grande differenza è la percentuale della componente “manodopera”. Per realizzare un telaio in Asia (Taiwan, Cina e ora Myanmar e Cambogia) bisogna comporre manualmente un puzzle di 400 tasselli di fogli di fibra di carbonio e ricorrere a stampi particolari, che richiedono il lavoro di più operai. Tutto ciò si traduce in un tempo medio di costruzione di un telaio che varia fra 26 e 30 ore. Ecco, noi dobbiamo scendere a 8 ore, per essere davvero competitivi. Ora siamo a circa 12 ore ed è un buon risultato.
Per raggiungerlo abbiamo lavorato su tre aspetti: i primi due sono materia prima e automazione. Dal cosiddetto preimpregnato (fibra di carbonio già amalgamata alla resina, una materia prima altamente lavorata e quindi costosa) siamo passati al filato, la vera e propria fibra di carbonio. È una scelta che, già a monte, ci dà un vantaggio in termini di costi, di quantitativi minimi e di opzioni specifiche in base al modello di bici. Per fare un esempio, è come se per fare una camicia si partisse dal filo anziché dal tessuto…
La stessa cosa vale per la resina, che scegliamo in base alle caratteristiche chimiche, in relazione al suo impiego.
Il ricorso alla fibra secca, svincolandosi dal preimpregnato, è legato alla scelta di lavorare la materia prima in un modo differente ossia con la tecnologia del “filament winding”, ossia l’avvolgimento della fibra su mandrini. Si tratta di un processo ampiamente conosciuto, che però noi abbiamo sviluppato in modo di poter creare geometrie che hanno forme complesse e stabili. Ogni tubo è costruito con quantità e trame di fibre differenti, a seconda della sua funzione, della rigidezza che si vuole ottenere e, quindi, del tipo di telaio. E il macchinario con cui lo si effettua è stato disegnato e costruito da noi, perché c’era l’esigenza di avvolgere il filato con la massima libertà di scelta, in termini di angoli e intrecci.
In questa fase della lavorazione, abbiamo già raggiunto anche l’obiettivo dell’automazione, poiché una sola persona è in grado di seguire fino a quattro macchine. Automazione che interesserà a breve anche un’altra fase della lavorazione, come vedremo più avanti.”
Qual è, invece, il terzo aspetto su cui si basa la transizione?
“Si tratta dell’efficienza energetica. Un aspetto meno legato ai tempi di lavorazione, ma che incide in modo pesante sui costi: basti pensare che, a differenza della fibra secca, il preimoregnato deve essere stoccato in freezer a una temperatura di -18°, per evitare che la resina si indurisca. Si tratta di una situazione che implica alti consumi di energia elettrica e ne vedremo altre nelle altre fasi del processo produttivo.
Da non sottovalutare è anche la ripercussione di questo aspetto sulla qualità del lavoro. Si pensi al fatto di avere ambienti con temperatura costante, senza sbalzi dovuti alle lavorazioni, o anche all’impegno fisico richiesto da operazioni come manovrare presse grosse e pesanti, rispetto alle nostre, che possono essere gestite con minimo sforzo da una sola persona.”
Come si arriva al prodotto finito?
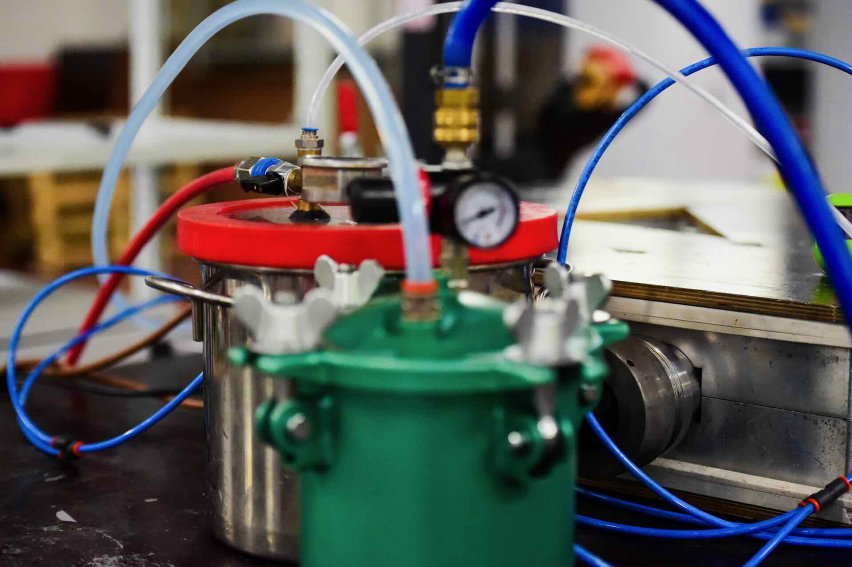
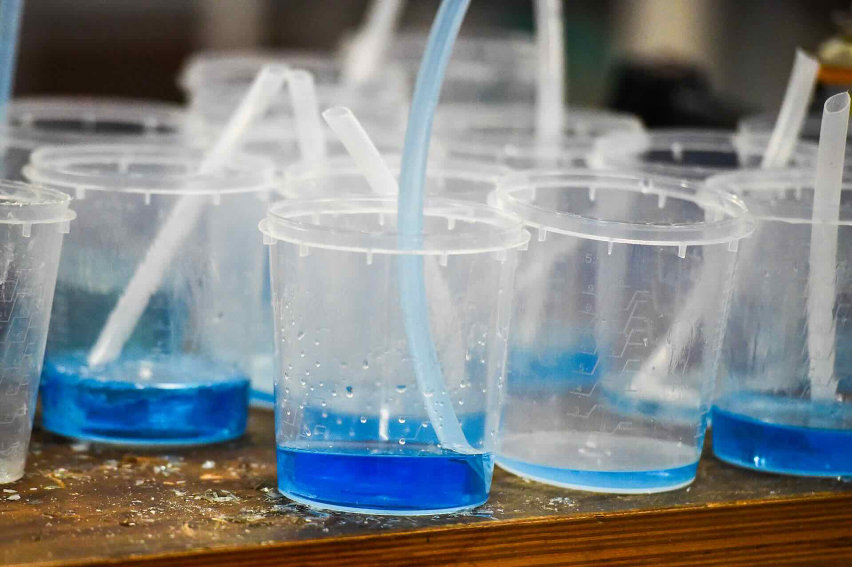
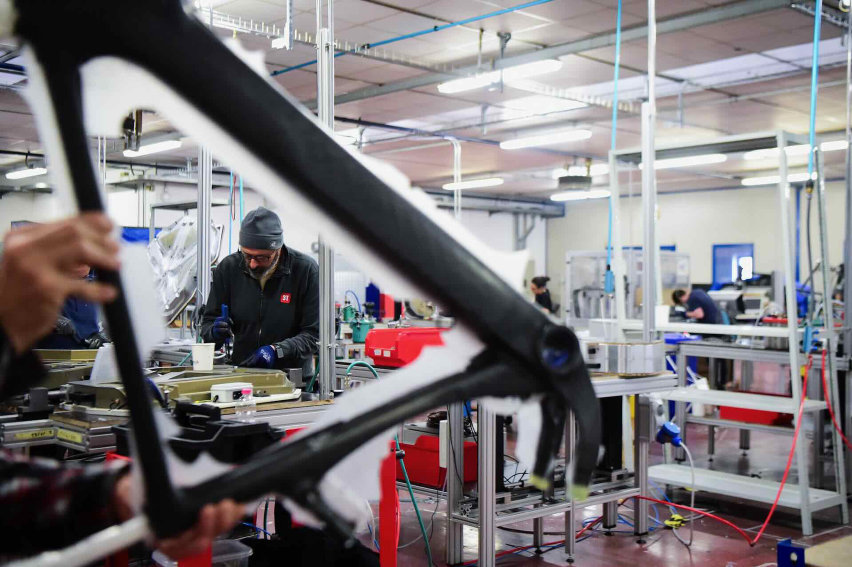
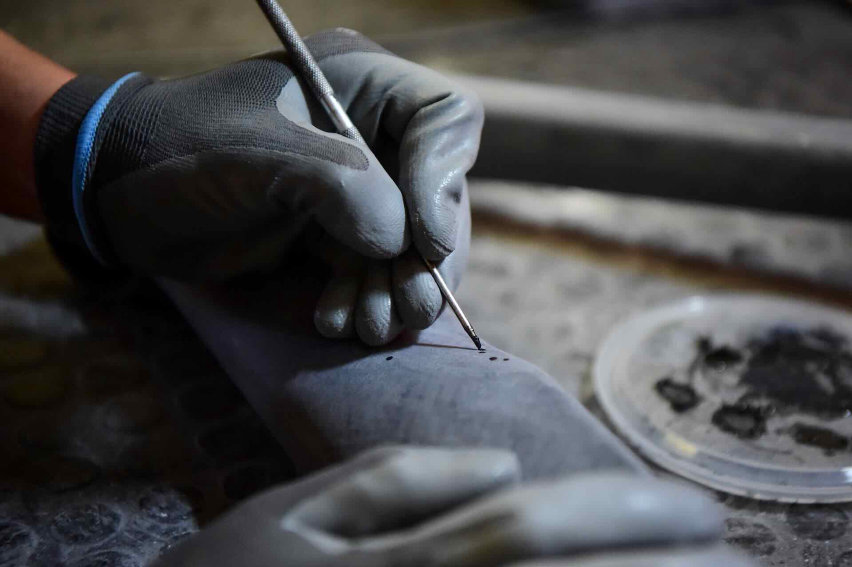
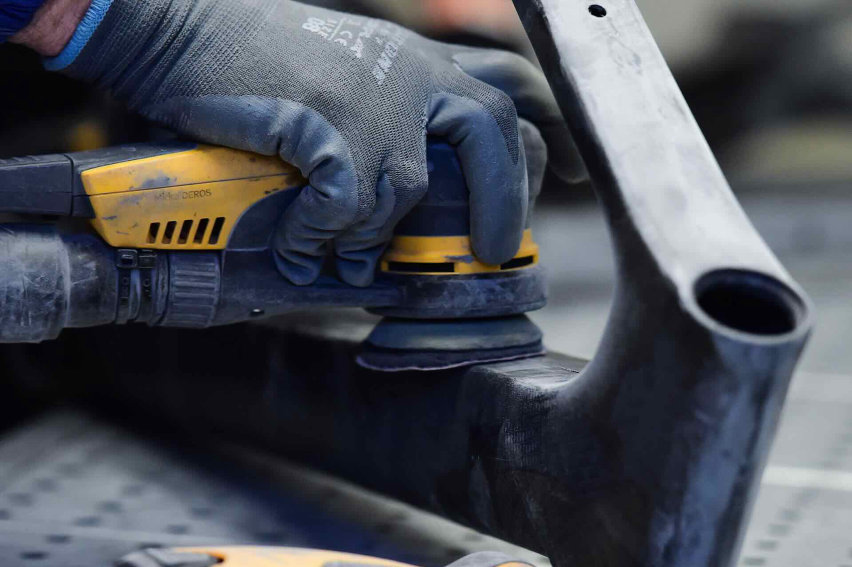
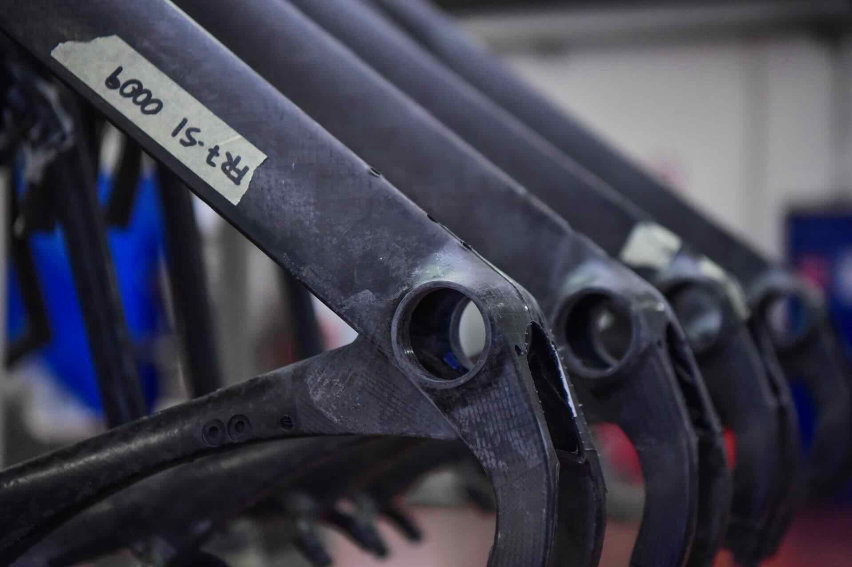
“Il percorso produttivo prosegue nella stanza di pre formatura, dove creiamo i pezzi che andranno nello stampo. Il 90% del telaio delle bici che produciamo qui è ottenuto con il metodo del filament winding, mentre il restante 10% è realizzato con la tecnologia tradizionale della sovrapposizione dei fogli.
È come se in questa lavorassimo unendo le competenze di un sarto e di un parrucchiere.
Si tratta del passaggio più importante dell’intero processo, che termina con l’operazione manuale di taglio e di “pettinatura”, in corrispondenza delle giunzioni, e con il pre assemblaggio, prima di passare allo stampaggio.
Operiamo secondo il processo RTM (Resin Transfer Molding, o stampaggio per infusione sottovuoto delle resine) in cui la struttura in fibra di carbonio è impregnata dalla resina, aspirata mediante il vuoto all’interno dello stampo.
Anche in questa fase, sono presenti due dei tre aspetti su cui abbiamo basato la filosofia produttiva. Materia prima: rispetto al preimpregnato, l’utilizzo di fibra secca consente di ricorrere a un processo di stampaggio che necessita pressioni e temperature inferiori. Inoltre, potendo scegliere la resina in base alle sue caratteristiche chimiche di reazione e indurimento, possiamo incidere ulteriormente sui tempi di permanenza del semilavorato nello stampo. Per fare un esempio pratico, se un telaio preimpregnato richiede una lavorazione di 3 ore ad almeno 120° a 3 ore, a noi bastano 80° e una ora e mezza. Ecco l’efficienza energetica...
Efficienza energetica che si manifesta anche al momento dell’incollaggio del carro: invece di usare una lampada a infrarossi da 2000 watt o un forno in cui inserire tutto il telaio, noi abbiamo costruito dei mini stampi riscaldati, che agiscono solo sulla sezione interessata e che consumano 175 watt.
I telai grezzi, ripuliti e forati, passano quindi all’ultima fase del processo produttivo, la finitura. Se nel pre stampaggio avevamo parrucchiere e sarto, qui siamo quasi dal dentista (sorride…, ndr).
Si tratta di un lavoro di precisione ancora manuale, ma presto la carteggiatura sarà realizzata da un robot che stiamo ultimando di testare. Ed è grazie anche all’automazione di questa fase che passeremo da 7/8 telai al giorno a 10/12, senza variare il numero di personale impiegato in produzione.
Termino con un’ultima annotazione. Un ulteriore vantaggio della fibra secca, rispetto al preimpregnato, è che i telai in “pre-preg” presentano spesso dei micro pori, una peculiarità solo estetica e senza ripercussioni strutturali, ma che obbliga a un’ulteriore lavorazione di stuccatura, prima della carteggiatura e, quasi obbligatoriamente, alla verniciatura.
Difficile che un telaio del far east sia proposto “nudo” come il nostro Project X, che con un paragone che mi piace molto, considero la trasposizione sul prodotto della nostra trasparenza come azienda.”
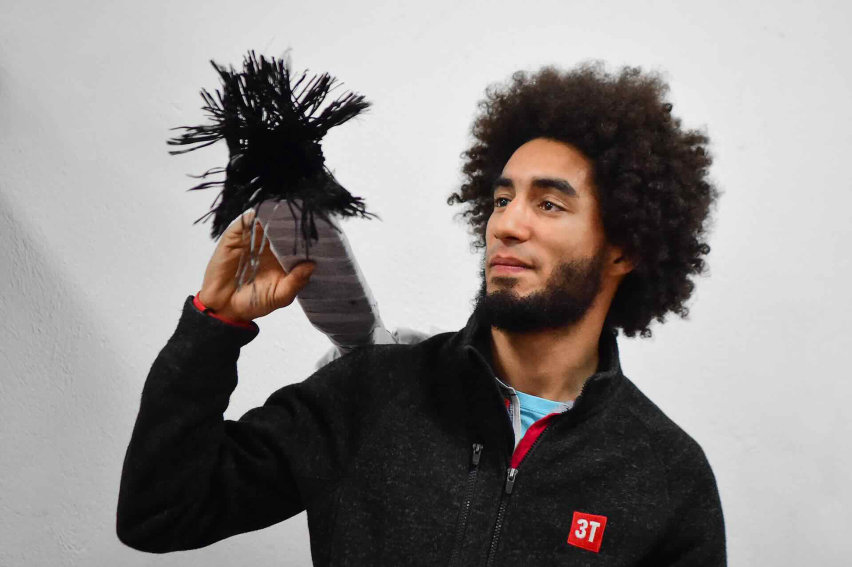